Go With The (Change Of) Flow: 3 Overlooked Tasks At WWTPs

By Kevin Westerling,
@KevinOnWater
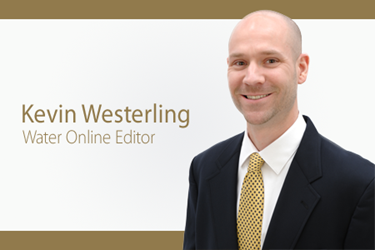
There are certain requirements incumbent upon the wastewater operator when the volume and nature of waste coming into the wastewater treatment plant (WWTP) changes — first and foremost of which is recognition.
That’s the easy part, as the changing levels of your equalization tank(s) should be a clear indicator. For volumetric increases, lab analysis and (hopefully) communication with local dischargers will help determine the nature of the waste. Decreases are decidedly more welcome in that they can result in plant savings, but both increases and decreases require additional action once the process flow rate is altered.
A change in the flow rate creates a chain reaction of related — but often overlooked — system requirements, according to Daniel Theobald, wastewater consultant and owner of Environmental Services. Theobald suggests these three follow-up tasks for optimized operations once your process flow rate changes:
- Adjust the chemical feed settings. The holding time within the process units will change with the process flow rate, so the amount of chemicals and/or chemical set points will need to be adjusted accordingly. Chemicals affected include coagulants, flocculants, and pH-adjustment chemicals.
- Account for changing process requirements. Operators may need to increase/decrease the time and labor dedicated to treating wastewater based on the volume and type of influent. If solids or sludge production decreases, for example, solids-handling runtime may decrease proportionally (and vice versa for increases).
-
Adjust for current (new) level of solids separation.
- In a conventional or inclined plate clarifier, you may need to change the pump settings to correspond to the new level of solids that require settling.
- In a dissolved air flotation (DAF) system, calibrate the air settings and the surface scraper speed according to the amount of solids and sludge present.
When it comes to efficient operations — where time is money and both are in short supply — awareness and responsiveness can help you save on precious resources. In light of this, Theobald’s message is don’t just “set it and forget it” when it comes to your process flow rate.
What further suggestions do you have for adjusting operations to flow rates? Can you name another often overlooked but important task at the plant?